The S.B.S One project
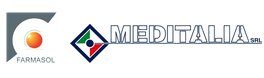
- Objectives of the project
- Activities of the project
- Major outputs and results of the project
- Environmental impacts
- Stakeholders
- Partnership
- Work programme
- Dissemination
- CIP Eco Innovation program
- Technical Progress
- Downloads & photos
The initiative will provide for an initial application, a new approach and an advanced process, integrated with eco-innovation and sustainability, to produce bags for biomedical use, in PVC free polymer extruded in a single layer (monolayer) absolutely eco/bio compatible: SBS (Sanitary Box Sustainable). These new products are alternative to the problematic monolayer PVC bags and the multilayer PVC-free bags and will overcome all the issues connected to these materials: PVC is toxic and harmful for the presence of plasticizers (carcinogenic) that can contaminate the content and concern big problems when burned for the destruction (dioxins and furans) but for his characteristics of low production costs and of simplicity of the productive cycle is the most used for the scope; multilayer PVC-free bags are nowadays the only alternative to the PVC but have some problems about the presence of non bio compatibles adhesives between the films (the problems that arise during the sterilization phase at 121 ° C, testing in progress of a multilayer product will last at least for another three years) and the high cost that limits a wide diffusion on the market.
These problems will be faced through the new polyolefin compounds.
The material to be validly propose will be able to overcome the judgment of the market because will has the characteristics of absolute biocompatibility, greater eco sustainability (the production waste is recyclable in the same cyle) and cost appropriate to a wide use. Moreover, the new product based on polyolefins will have a lower energy footprint and, due to its better processability (mainly PE with PP additions) will possess a lower CO2 footprint compared to plasticized PVC, as well as a lower embodied energy.
Starting from the optimization of the polymeric system for the specific needs of process and products, the project will proceed to the selection of polymer blends suitable. The candidate materials are those belonging to the family of poly-olefins, with particular regard to the polyethylene and polypropylene in the available formulations. Blends based on LLDPE (Linear Low Density Polyethylene), M-LLDPE (Linear Low Density Polyethylene Metallocenic), HDPE (High Density Polyethylene), PP (Polypropylene) will be used, and the mixing of different polymers will allow to modify the characteristics of the materials like cristallinity and hence mechanical properties. The blends will have excellent processability and properties potentially compatible with the requirements of the products to be realized, provided that appropriate parameters and conditions in film processing are taken.
Thus, the project will then focus in particular on the blending and forming process conditions. Poly-olefins and their copolymers will be produced in a highly efficient gas-phase or liquid, through a catalyst without using any organic solvent. Moreover, thanks to its composition, poly-olefins thermal disposal will not lead to the formation of toxic chemicals.
In order to achieve the expected objectives at an industrial scale, the following activities will be performed:
1) preparation of polyolefin blends;
2) modification of forming parameters (bubble extrusion);
3) modification of joining parameters for bags formation and tubes positioning; verification of joints homogeneity;
4) adaptation of packaging station (external safety bag);
5) filling tests with dialysis or emoderivatives fluids and modification of equipment to account for the different properties of the finished empty bag;
6) sterilization process setup and optimization to account for the lower maximum bearable temperature of the new bags;
7) recyclability tests and evaluation of environmental indicators + process energy and mass balance.
The main expected outputs will be safer and non harmfully recyclable biomedical bags, polyolefin based, for dialysis and emoderivatives and chemotherapy fluids, presenting a maximum embodied energy of 70 MJ/kg and a CO2 footprint lower than 25 kg CO2/kg, values which are approximately 15% lower than current PVC products. The new bags will have low haze and high transparency, with tensile strength in the 16-19 MPa range, for an estimated elongation at break of 200-400%. Glass transition temperature will be in the range -30/-10 ° C, allowing to weld the materials between 160 and 220°C, maintaining a low oxygen permeability (approx. 400 cm3 / (m2 x day x bar), low water vapor permeability (approx. 4.5 g / (m2 x day x bar) and biocompatibility (UNI EN 30993).
Moreover, no releasable plasticizer will be used, thus conferring to the new products the highest safety in use and during thermal destruction or recycling. Competitiveness in terms of costs of the new products will derive also from the better processability and lower overall raw materials cost.
The major environmental impacts related to the development of the project will be:
- Lower embodied energy respect to the actual products in order of 70 MJ/Kg; considering an average production of the company of 2.500.000 Kg/year, this means a reduction of the embodied energy of 175.000.000 MJ/year;
- Lower carbon footprint of 25 KgCO2/kg, that is 62.500.000 Kg/year for the company, at the end of the project;
- The new products will have all the characteristics to be introduced positively on the market and then an high potential for replicability.
The expected results regarding the environmental benefits will deal with the impacts associated with the main process stages form a life-cycle perspective, by the mean of the "cradle to grave" approach. In terms of utilization and acquisition of raw materials the project will improve the employment of PVC-free materials. Indeed the main environmental benefits will involve the adoption of PVC-free materials for the biomedical bags manufacturing, thus achieving the reduction of embodied energy and CO2 footprint (it must be taken into account that the comparison, rather than on a mss basis, should be performed on a volume basis, being the geometry of the bags fixed, but the density of the new blends significantly lower).
Moreover, in terms of end of life treatment from an LCA perspective, the new process will allow to immediately recycle the cutting scraps in the same manufacturing cycle of bags, by simple re-insertion in the blending apparatus, magistra case of industrial symbiosis. Moreover, polyolefins do not present recycling risks, either by simple remelting or by combustion, and this will allow to recover energy and improve the raw material utilization in a life cycle approach.
The mail objective of the project is the elimination of the PVC from the biomedical application context, opening definitively the way to the banning of the PVC also in other sectors that involve the health, the alimentation and all that create direct contacts with the Polyvinyl chloride.
The argument is very serious, considering the hazard of Polyvinyl chloride, whose bibliography is full of warnings ("Carcinogenicity" and the deadly impact on health and air pollution for the release of dioxins).
The target groups are the sector organizations and the public administrations of the sanitary and biomedical field and the private clinics that should become a winner trailblazer for their better and careful flexibility, which are of major interest to stakeholders on the local, regional, national, European and global levels. The innovative solution proposed will result of particular interests for the whole public and private sector healthcare providers, especially those involved in safer and more environmentally-friendly solutions in plastics as well as in chemicals.
Among the target groups, also regulatory bodies can be involved as well as the consumers associations, since the health benefits deriving from the lack of dangerous chemicals in the bags could lead to a change in the opinion and starting actions to support new products in the field. Also biomedical devices manufacturers can be interested, since they could benefit from the transfer of the new polymeric mixture to their product range, further decreasing the medical uses of the potentially dangerous and difficult to dispose PVC
The consortium gathers two actors synergically operating in the biomedical bags sector, one dedicated to polymer transformation into films and bags (Meditalia), and the other starting from bags and performing filling, sealing, sterilization and packaging operations (Farmasol). The opportunity of having an innovative polymer blend used for PVC-free bags industrially tested not only in bags forming, but also in the bags post-processing by filling and sealing is guaranteed by this consortium as the two participants, operating on two aspects of the same problem, will work together to bring PVC-free bags to an industrial reality.
Meditalia S.r.l. is an international company, its activity is addressed to the production of polymeric alloys in PVC for the medical sector with features and qualitative standards adequate to the prescriptions of the international pharmacopoeia. The company has a laboratory equipped, recognized and certificated by the Ministry of University and Research (MIUR in Rome), to ensure that each batch of incoming materials and finished product meets the requirements of international pharmacopoeias and then the possible application in medical field. The wide range of formulations of PVC granules , the first step in the chain of processing, is done in a modern granulation plant. The department "extrusion tubes and pipes" is a large area of 250 m2 (clean room class 10.000) subject, every 6 months, to controls to check microbial and particle contamination and is equipped with modern and validated plants for the extrusion and wrapping of the product which allow you to make films and tubes perfectly suitable for the intended uses.
The pipe's production plant, with high technology and productivity, is provided with laser detector, in this way it is possible to control the dimension (inside diameter, outside diameter ,wall thickness) to ensure a continuous monitoring of the quality of the finished product.
The department "production of sacks" is an area of 600 m2 (clean room class 10.000), subject to control every 6 months to verify microbial contamination of air, surfaces and air particles.
The department is equipped with modern and efficient automatic systems for the production of sacks used to contain solutions for medical use and the production of the medical device "Kifarm sack". The environment filtered with 99.99% HEPA filters is overpressure compared to a large area 150 m2 100,000 class in which the product, packaged in double polyethylene sack is transferred to boxing. For the final packaging are used cardboard boxes which ensure the preservation of quality during long transport. The warehouse takes shape on an area over 2000 m2, equipped with thermo areas.
Farmasol S.r.l. is a young company that started is activities in late 2005.
The company was born by the will of the two current directors, Dr. Vito Rocco Miraglia and Dr. Pasquale Ottati, to join their experience in the pharmaceutical and biomedical industries, to create a successful reality in the South of Italy.
Farmasol has specialized in the production of pharmaceutical products for hospital use and in particular biomedical bags used to contain solutions for haemodialysis.
Now Farmasol produces about 2.000.000 bags per year in two different size (3,8 litres and 5 litres) in his new factory in Baragiano, near Potenza. The new factory has a size of 3000 sqm and has allowed to automate the various stage of production and increasing the quality standards of processes and products. During 2010 a 130 kW photovoltaic plant was realized contributing to significantly reduce energy costs and environmental impact.
The programme will have an interconnected structure, replicating the steps necessary to arrive to a completely functioning production line for biomedical bags and a production line to industrially post process (filling, sealing, sterilizing, packaging) the new bags. For this reason, the programme activity has been divided into subsequent workpackages which separately follow the flow of the product during manufacturing. Each workpackage will be dedicated to the realization of one component or sub-system of the final plants, which then will be assembled and tested at each proposers' site. The programme will start by realizing, at Meditalia site, the required polyolefin blends and dedicated blending system (WP2). The project will continue with the modification of the Meditalia's bubble extrusion equipment (WP3) to account for the different properties of the starting material. The obtainment of the first films will serve to continue the ageing tests on this new materials, at Farmasol's site, providing feedback to Meditalia to improve or alter the original blends. On the optimized blend, already blow moulded in coupled films, cutting and joining operations will be performed by a modified equipment (WP4), according to the new materials thermal properties and allowing to achieve the first testing pre-series of PVC-free bags manufactured at Meditalia's site. Such bags will be used in a dedicated modified filling line at Farmasol plants, in order to verify the correctness of the dimensioning of the tools and to further optimise filling and sealing operations on the new materials. The output will be PVC-free bags filled with saline solution (WP6), which will be artificially contaminated to study and optimize the industrial sterilization (WP7) of the new bags, at Farmasol's site. Meanwhile, at Meditalia's site, the cleaning and packaging operations will be implemented on the manufacturing line (WP5), leading to the first commercial-like series of the new polyolefinic bags. On the finished product, recycling tests by moth remelting and combustion will be performed, and used, with a life cycle approach, to evaluate the environmental performance of the new bags (WP8). An LCA study by the mean of apposite software and suitable database internationally recognized will be performed, taking into account also the transportation and other possible environmental burdens. The main environmental indicators will be calculated. The packaged bags, manufactured by Meditalia, will be used by Farmasol to start the production of commercial-like saline solution bags and emoderivatives bags, comprehensive of the new label indicating the eco-friendliness of the new product. The project will be completed by the institutional WP as Management (WP1), Business Plan and Exploitation (WP9), Dissemination Activities (WP10).
Project Logo
Notice boards realized
Letterhead with logo
Participation at the fair "Medica" in Dusseldorf in November 2014 The project has been presented with very good feedbacks and the collection of several interested contacts for future collaboration.
New logo realized for the project
Launched in 2008, the Eco-innovation initiative is part of the EU's Entrepreneurship and Innovation Programme (EIP), set up to support innovation among SMEs and to improve their competitiveness. It is included in the EIP's annual work programmes. The EIP is part of the wider Competitiveness and Innovation Framework Programme (CIP) aimed at encouraging the competitiveness of European companies, in particular SMEs. The Eco-innovation initiative is one of the measures designed to implement the EU's Eco-innovation Action Plan (EcoAP) that seeks to boost environmental technologies while strengthening economic growth and competitiveness.
The eco-innovation initiative bridges the gap between research and the market. It helps good ideas for innovative products, services and processes that protect the environment become fully-fledged commercial prospects, ready for use by business and industry. In doing so the initiative not only helps the EU meet its environmental objectives but also boosts economic growth.
Eco-innovation is about reducing our environmental impact and making better use of resources. This means developing products, techniques, services and processes that reduce CO2 emissions, use resources efficiently, promote recycling and so on. There are five main strands to this initiative:
- Materials recycling and recycling processes;
- Sustainable building products;
- Food and drink sector;
- Water efficiency, treatment and distribution;
- Greening business.
The EU is looking to maximise the impact of Eco-innovation and make every euro go as far as possible. The best Eco-innovation projects are those that can be replicated across the EU.
7 Eco-innovation projects are not research projects. The ideas must be developed, feasible and also viable in the long-term to qualify for funding.
Eco-innovation represents a key opportunity to establish Europe's leading role in overcoming the world's sustainability challenges while making Europe's economy even stronger and more competitive.
The first activities carried out were the creation of a management team, with both Meditalia and Farmasol members, for the management and the monitoring of the project progress. Two separated accounting software, Excel-based, have been created for the project, one for the personnel management, including the creation of the timesheets, and one for the expenses accounting. The blends definition activity started regularly and is finished. Various tests have been carried out on the process and some issues were encountered in the bubble extrusion application. The work done is important and satisfactory; some activities carried out permitted, moreover, to save time in the future work. Various tests have been made with several blends composition, using initially the equipment already present in partners? places and updating some of these to comply with the new blends. The two partners exchanged data regarding the properties that the blends would have in order to optimize the composition not only for bags manufacturing, but also for subsequent handling, filling and sealing operations. Varying each parameters and configuring the systems, finally the right blend compositions have been identified. The mixing station is fully functioning with new parameters for the new blends, linked to the grinding reactors which have been made expressly for the innovation proposed. Initially, the better extrusion equipment able to treat the new blends identified to obtain the expected films proved to be a cast film plant with flat head. Compared with the bubble extrusion, this technology proved to guarantee better homogeneity of thickness and good optical properties and to permit to avoid problems on bubble stability and breakage of the spindle, which do not permit continuous productions. A set of configuration parameters of the extrusion film forming able to obtain a stable coil has been achieved in a continuous way. After these, started the studies about how to optimize the forming process to comply with the required productivity. During this phase, some changes were tried on blends composition starting from new ideas come out. Given the results already achieved, fully complying with the project objectives and activities, and the time saved till now, some changes were tried in order to adapt the process to a bubble extrusion system, to fit with internal equipment, but especially to have a complete possibility to spread the technology identified to all the possible existing processes and systems, i.e. flat head or bubble extrusion. Good results have been achieved without wasting project time and we are confident to achieved the same results as with the flat head system. The design and realization of new clamping, conveying and holding systems to handle the new materials have been carried out as well as the definition of the modification on the existing post-processing equipment for filling, sealing and packaging.